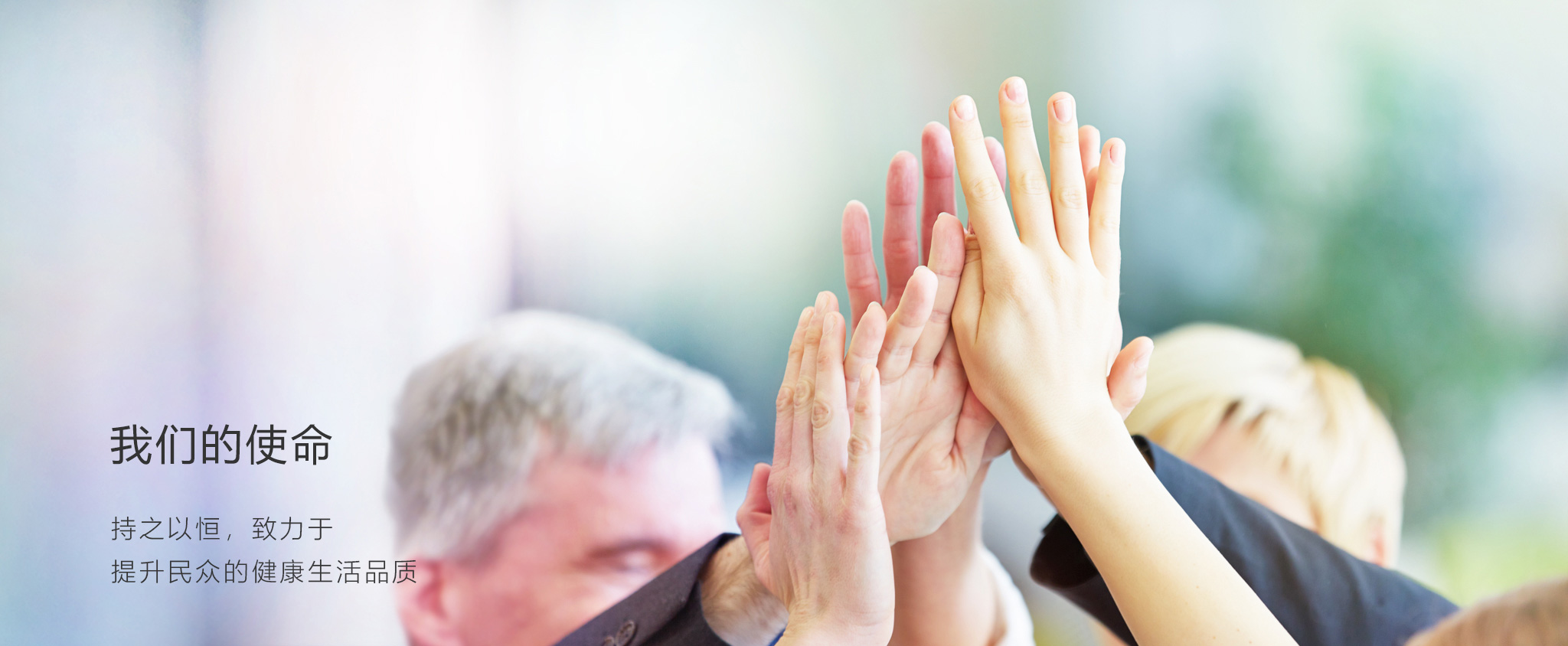
1、CNC 区, Controlled/Not Classified ,受控但不分级别,区域易于清洁,进出受控制并且空气经过过滤,如人员进入一般生产区需要更衣要控制,这个区域需要处于受控状态;再如废弃物出口、气锁间、洗瓶前瓶子准备间、工艺支持区等。
2、题主是否想询问“原料药生产车间非洁净区可以使用吗”?不可以。
3、药厂洁净室或洁净区,是指需要控制粉尘颗粒和微生物污染的区域。 按照GMP设计要求,药厂生产厂区通常分为一般生产区(无洁净要求)、控制区(100000级、300000级)、洁净区(10000级)和无菌区(100级)。
4、洁净区生产环境除有一般区生产环境的要求,还应洁净区级别符合相应药品要求,洁净区温度:18℃―26℃;相对湿度:45%―65%。洁净区与非洁净区之间、不同级别洁净区之间的压差应当不低于10帕,空气洁净级别不同的洁净室(区)之间的压差大于5帕,每班记录。
5、洁净室是指将一定空间范围内之空气中的微粒子、有害空气、细菌等之污染物排除,并将室内之温度、洁净度、室内压力、气流速度与气流分布、噪音振动及照明、静电控制在某一需求范围内,而所给予特别设计之房间。
1、通过缓冲室、传递窗( 柜)传。根据物料进出洁净区标准操作规程,不可灭菌药品生产用物料从 B 级洁净区 到一般生产区,必须经缓冲室、传递窗( 柜)传出去。
2、定义不同:一般生产区指的是和生活区相区别的生产场地不一定是洁净区;洁净区指的是部分生产工艺需要的严格的生产条件。在洁净厂房设计规范GB50073-2013的定义为:空气悬浮粒子浓度受控的限定空间。它的建造和使用应减少空间内诱入、产生及滞留粒子。
3、不是。因为生产区分为一般生产区和洁净级别生产区,只有洁净区才分为A级、B级、C级、D级。
4、药厂洁净区划分为A、B、C、D四个级别,其中A级为高风险操作区,包括灌装区、放置胶塞桶、敞口安瓿瓶、敞口西林瓶的区域及无菌装配或连接操作的区域。
1、可分为以下4个级别:A级 高风险操作区,如:灌装区、放置胶塞桶、敞口安瓿瓶、敞口西林瓶的区域及无菌装配或连接操作的区域。通常用层流操作台(罩)来维持该区的环境状态。层流系统在其工作区域必须均匀送风,风速为0.36-0.54m/s(指导值)。应有数据证明层流的状态并须验证。
2、药厂洁净区划分为A、B、C、D四个级别,其中A级为高风险操作区,包括灌装区、放置胶塞桶、敞口安瓿瓶、敞口西林瓶的区域及无菌装配或连接操作的区域。
3、药厂可分为以下4个级别:A级:高风险操作区,如:灌装区、放置胶塞桶、敞口安瓿瓶、敞口西林瓶的区域及无菌装配或连接操作的区域。通常用层流操作台(罩)来维持该区的环境状态。层流系统在其工作区域必须均匀送风,风速为0.36-0.54m/s(指导值)。应有数据证明层流的状态并须验证。
4、万级; 微生物最大允许数:1000 浮游菌/立方米;适用场合:丸剂、颗粒包装车间。10万级;微生物最大允许数:500浮游菌/立方米; 适用场合:注射剂浓配车间。1万级;微生物最大允许数:100浮游菌/立方米 ;适用场合:小容量注射剂灌装车间,直接接触药品的包装材料最终处理车间。
5、人员进入洁净区必需遵循下列要求:更衣室是操作者进入生产岗位更衣的场所,非生产操作人员未经部门负责人允许不得擅自进入。进出更衣室必须先换上工作鞋,更换下的鞋应存放在指定的鞋架上,不得随意放置。进出更衣室必须关好一道门,违者将给予处罚。
1、洁净室不可能做到真正的无尘,它只是根据不同的生产车间的要求,做到不同的洁净等级。所以洁净度指的就是洁净等级。常用的洁净等级标准,按照美国联邦209E标准,1级10级百级千级万级十万级等等。
2、是指专业的技术人员的工作环境无尘车间、无尘室或清净室。洁净室的主要功能为室内污染控制,没有洁净室,污染敏感零件不可能批量生产。
3、洁净室(区)是指需要对尘粒及微生物含量进行控制的房间(区域)。进入洁净室(区)的空气必须净化,并根据生产工艺要求划分空气洁净级别。洁净室(区)内空气的微生物数和尘粒数应该定期监测并记录存档。药品生产洁净室(区)的空气洁净度划分为四个级别,即100级、1万级、10万级、30万级。
1、生产过程结束后,各工序应按照清场程序对生产现场及设备及时进行清场。清场后由质量监督管理人员检查清场效果,合格后在“清场合格证”正本和副本规定位置签名。
2、药品质量监控管理方法:质量体系要规范,全面实施才能去生产。要求人机料法环,缺掉任何都要有风险。生产现场要监管,避免混淆和交叉污染。第一质量目标要明确,会议交流评审少不了。织机构应健全,培训到位岗位明确了。生产环境要监控,莫忘表面和五指手套。
3、在生产过程中,企业需要按照GMP的要求进行生产操作,如控制温度、湿度、时间等参数,确保生产出的药品符合质量标准。最后,在药品出厂前,企业还需要进行成品检验和放行审核,确保药品的安全性和有效性。总之,药品生产质量管理规范是保障药品质量和安全的重要制度。
4、其次,药品生产的质量管理规范是确保药品质量的关键环节。这包括制定生产工艺规程、建立质量控制体系、实施生产过程中的质量监控等。药品生产企业必须按照国家药品生产质量管理规范(GMP)进行生产,确保生产环境的洁净度、设备的运行状况以及原材料的质量等都符合规定要求。
5、质量保证与质量控制:质量保证是通过预防措施来确保药品质量,如定期进行内部审计、风险评估和质量改进等。质量控制则是对药品生产过程中的关键控制点进行实时监控,确保每一步操作都符合预定标准。 人员培训与管理:药品生产涉及的专业性强,要求员工具备相应的专业知识和技能。
6、质量管理体系(QMS):质量管理体系是药品生产中最为关键的管理体系之一。它涵盖了质量保证(QA)和质量控制(QC)两个方面。质量保证包括制定和执行质量政策、质量目标、质量手册以及各项质量程序等。质量控制则包括生产过程中的监测、分析、验证和确认,确保产品符合标准和规定。